Gas fitting is an essential aspect of home and commercial building safety, ensuring that gas appliances and lines operate efficiently and safely. One crucial procedure within gas fitting is pressure testing, a process that can prevent dangerous leaks and ensure the integrity of gas systems. In this blog, we’ll dive deep into what pressure testing is, why it’s important, and how it’s performed.
What is Pressure Testing?
Pressure testing is a method used to determine if a gas system is functioning correctly and safely. It involves filling the gas system with a test medium, usually air or nitrogen, and then applying pressure to check for leaks. This process is vital because gas leaks can pose significant safety risks, including explosions, fires, and poisoning.
The main goal of pressure testing is to ensure that the gas system is airtight and that no gas will escape during regular use. This is especially important during installation or repair work, as it helps to verify that all joints, connections, and components are secure and functioning properly.
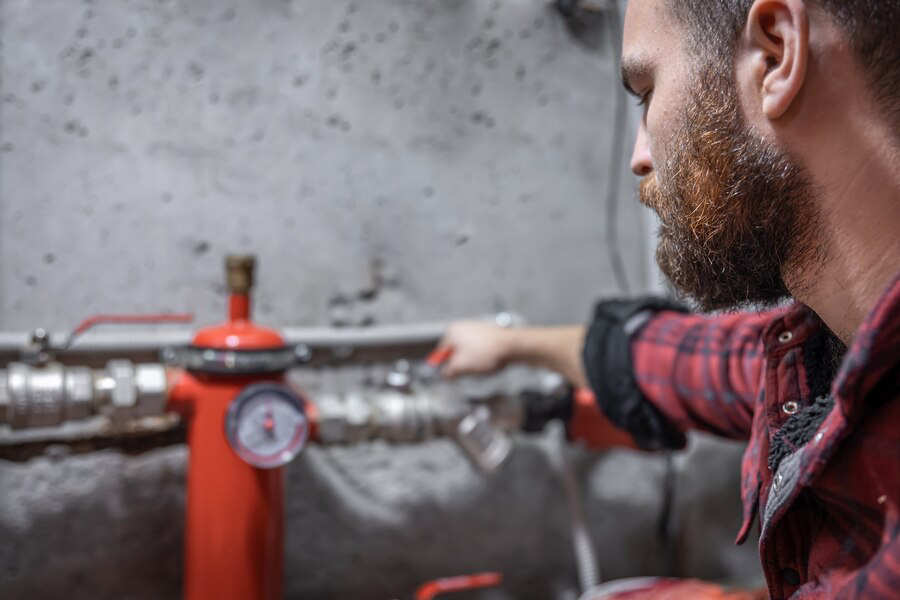
Why is Pressure Testing Important?
Safety First
The primary reason for pressure testing is to ensure safety. Gas is an inherently flammable substance, and even the smallest leak can lead to severe consequences such as explosions, fires, or toxic exposure. By conducting pressure tests, any leaks can be identified and repaired promptly, significantly reducing the risk of dangerous incidents and protecting both people and property.
Compliance with Regulations
Pressure testing is often mandated by law in various regions for both new gas installations and existing repairs. Adhering to these regulations is crucial as it ensures that the gas system complies with established safety standards. Proper compliance not only helps to avoid hefty fines or legal penalties but also assures that the installation or repair meets industry safety requirements, providing peace of mind to all parties involved.
System Efficiency
A gas system that is free from leaks operates more efficiently, which translates to better performance of gas appliances and overall energy use. Pressure testing helps to confirm that there are no leaks affecting the system’s operation. By maintaining the system’s integrity, energy consumption can be optimized, leading to potential savings on utility bills and improved performance of gas-powered equipment.
Preventing Costly Repairs
Early detection of leaks through pressure testing can prevent more significant and costly issues from arising in the future. Minor leaks, if not addressed promptly, can escalate into major problems requiring expensive repairs or even complete system replacements. Regular pressure testing helps to identify and fix small issues before they develop into major faults, ultimately saving homeowners and businesses from potentially high repair costs and disruptions.
How is Pressure Testing Performed?
Preparation
- Shutting Off the Gas Supply: To ensure a safe pressure test, the gas supply must be completely shut off. This step prevents any gas from entering the system during testing, ensuring that the test results are accurate and that there’s no risk of gas leaks during the process.
- Isolating the System: All appliances and components that are not part of the pressure test should be isolated or removed. This step helps to focus the test on the specific system being evaluated and prevents interference from other parts of the gas system.
- Inspecting the System: Before starting the pressure test, a thorough visual inspection of the gas system is performed. This inspection helps to identify any obvious issues or damage that might affect the accuracy of the pressure test or compromise system safety.
Filling the System
After preparation, the gas system is filled with a test medium. Air is typically used for this purpose, but in some cases, nitrogen may be employed due to its stable and non-reactive nature. The test medium is introduced through a dedicated valve to ensure proper filing.
Applying Pressure
Once the system is filled with the test medium, it is pressurized to a level that exceeds the normal operating pressure. This increased pressure helps to reveal any potential leaks, as even minor leaks become more apparent under higher pressure conditions.
Monitoring for Leaks
A pressure gauge is used to monitor the pressure within the system. If the pressure drops, it indicates a potential leak. Continuous monitoring helps to detect and address any leaks promptly before they become serious issues.
Adjustments and Repairs
If any leaks are detected during the test, the affected areas need to be repaired or adjusted. After making the necessary repairs, the system should be re-tested to ensure that all issues have been resolved and that the system is now leak-free.
Final Checks
- Restoring the Gas Supply: After a successful pressure test, the gas supply is restored. The system is then carefully monitored to ensure that it operates correctly and that no new issues arise during regular operation.
- Final Inspection: A final inspection is conducted to confirm that the gas system is functioning properly and safely. This inspection ensures that all repairs were effective and that the system is full
Common Issues Detected During Pressure Testing
Loose Connections
Loose or inadequately fitted connections are frequent culprits of gas leaks. During pressure testing, these connections are evaluated under increased pressure, making any loose joints or fittings more apparent. Identifying and tightening these connections prevents potential leaks and ensures the system’s overall integrity.
Cracked Pipes
Cracked pipes are a common issue that can lead to gas leaks. These cracks might develop due to factors like aging, corrosion, or physical damage. Pressure testing can reveal these cracks by applying pressure that exposes leaks, allowing for prompt repairs and preventing further system deterioration.
Faulty Valves
Valves that fail to seal properly are another common problem that pressure testing can uncover. Faulty valves can result in leaks or inefficient system performance. By testing the system under pressure, any valves that don’t close tightly or function correctly can be identified and replaced to maintain system reliability.
Damaged Seals
Seals and gaskets play a crucial role in preventing leaks by creating airtight seals. Over time, these components can degrade or become damaged, leading to leaks. Pressure testing helps in identifying any damaged or worn seals, allowing for timely replacement and ensuring the gas system remains leak-free.
Best Practices for Pressure Testing
Hire a Qualified Professional
Pressure testing should be performed by a qualified gas fitter or technician. They have the necessary training and equipment to carry out the test safely and accurately.
Follow Safety Guidelines
Ensure that all safety guidelines and regulations are followed during pressure testing. This includes wearing appropriate protective gear and following procedures for handling test media.
Regular Maintenance
Regular pressure testing as part of a maintenance schedule helps to keep the gas system in good condition. This proactive approach can prevent issues before they arise.
Documenting Results
Keep detailed records of all pressure tests, including the results and any repairs made. This documentation can be useful for future reference and for ensuring compliance with regulations.
Why Accurate Gas Fitting Pressure Testing Is Crucial
Accurate gas fitting pressure testing is essential to ensure the safety and reliability of your gas system. Pressure testing helps identify any potential leaks or weaknesses in the gas lines before they become serious problems. A well-conducted test verifies that the system can handle the required pressure levels without risk of failure, which is critical for preventing dangerous leaks and ensuring compliance with safety regulations.
Beyond safety, pressure testing also contributes to the longevity of your gas system. By detecting issues early, you can address them promptly and avoid costly repairs or replacements in the future. Regular pressure testing is a proactive measure that supports both the functionality and durability of your gas fittings.
Pressure Testing Gas Fittings: What You Need to Know
Pressure testing gas fittings involves evaluating the system’s ability to maintain pressure without leaks. This process is crucial for ensuring the integrity of your gas lines and preventing potentially hazardous situations. A pressure test typically involves applying a specific amount of pressure to the gas lines and monitoring for any drops or irregularities that might indicate a leak or failure in the system.
Understanding the importance of pressure testing helps you appreciate why it should be performed by a professional. Technicians use specialized equipment to carry out accurate tests and interpret the results. Regular pressure testing is a key component in maintaining a safe and efficient gas system, making it an essential aspect of routine gas maintenance.
Conclusion
Understanding gas fitting pressure testing is vital for maintaining a safe and efficient gas system. Accurate pressure testing ensures that gas lines are free from leaks and capable of handling the required pressure, thereby preventing potential hazards and ensuring compliance with safety standards. EZI Plumbing in Valley Bay, AU, offers expert pressure testing services to safeguard the integrity of gas systems. For reliable and thorough gas fitting inspections, contact EZI Plumbing at 0448467788. Trust EZI Plumbing to ensure your gas system remains safe and functional through meticulous pressure testing and professional service.